A Complete Guide to Manufacturing Accounting for Beginners
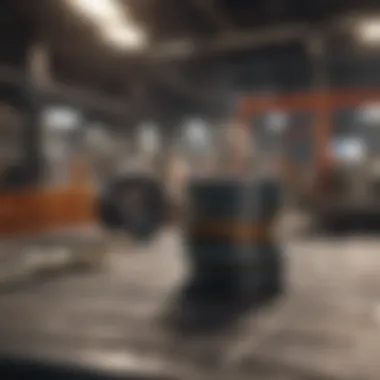
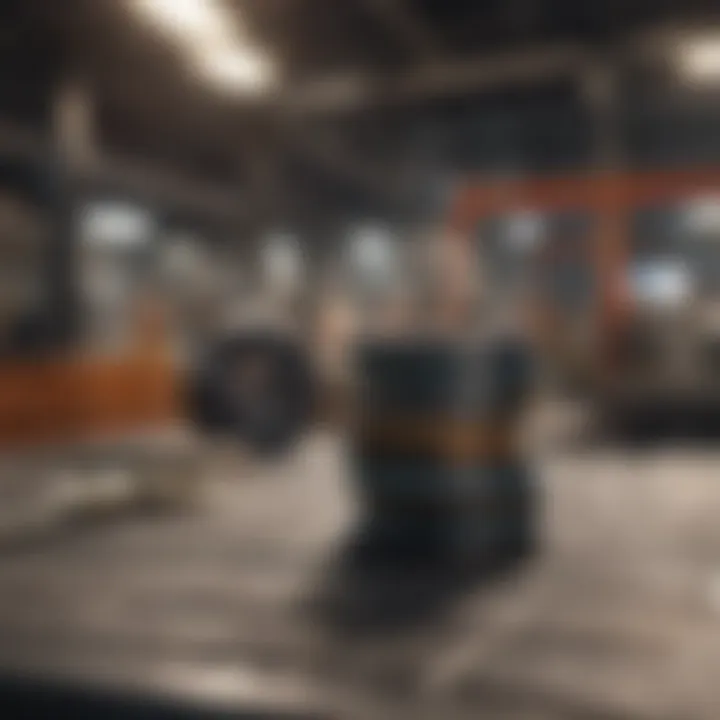
Intro
Manufacturing accounting can seem complex, especially to those lacking a background in finance. This section aims to clarify what manufacturing accounting entails and why it matters. Understanding this specific branch of accounting is crucial for anyone involved in production. It not only aids in tracking costs but also helps in decision-making processes.
This guide will elaborate on core concepts and practical techniques used in manufacturing accounting. Keywords like cost allocation, product costing, budgeting, and forecasting will frequently arise. These terms will become pivotal as we explore together the essential characteristics that define effective manufacturing accounting.
Ultimately, the goal is to empower individuals with the knowledge to effectively manage their manufacturing operations financially.
Budgeting Techniques
A well-crafted budget serves as a blueprint for financial performance in manufacturing accounting. It guides the allocation of resources toward essential areas while shedding light on spending patterns.
Creating a Personal Budget
Creating a budget begins with identifying all sources of income. This may include wages, benefits, or other forms of revenue. Subtract total expenses from total income to assess financial health. Structuring a budget involves listing fixed costs, such as salaries and rent, alongside variable costs, like materials and marketing.
Tracking Expenses Effectively
Tracking expenses is key to maintaining a budget. Using financial software such as QuickBooks or Excel can substantially simplify this task. Regular reviews enable better insights into where costs can be trimmed without impacting productivity or quality. The aim here is to ensure that money is not wasted and each dollar aids operational efficiency.
Setting Realistic Financial Goals
Realistic financial goals are essential for guiding manufacturing accounting practices. These goals should align with overall business strategy. They must also be measurable and achievable within specific timeframes. This parallels strategic planning, providing a focused roadmap ensuring accountability on all operational fronts.
Manufacturing accounting transforms financial practices, not only ensuring costs are monitored but driving strategic growth.
Foreword to Manufacturing Accounting
Manufacturing accounting is a distinctive discipline that assists manufacturers in analyzing and managing their finances effectively. Understanding this area is beneficial for stakeholders at all levels, particularly those who are not experts in finance or accounting. Embracing manufacturing accounting gives clarity on resource allocation, production efficiency, and overall business sustainability. This section highlights what makes this field essential.
Importance of Accounting in Manufacturing
Accounting serves as the backbone of the manufacturing process. It provides critical data that informs strategic business decisions. For manufacturers, maintaining accurate records of financial transactions allows for better tracking of costs, revenues, and cash flows. Understanding these elements is imperative for the following reasons:
- Cost Control: Effective accounting helps in identifying high-cost areas in production, enabling manufacturers to implement cost-saving measures.
- Budget Management: By tracking financial performance, businesses can create realistic budgets that reflect their capabilities and market conditions.
- Performance Evaluation: Monthly and quarterly financial statements offer insights into how well the business is performing against its goals.
Thus, a robust accounting framework not only aids compliance with laws and regulations but also positions a manufacturing company for success in a competitive landscape.
Overview of Manufacturing Costs
Manufacturing costs encompass the total expenses incurred in the creation of products. These costs can be categorized into different types, signaling where the money goes within the production cycle. The two primary categories are:
- Direct Costs: These costs can be traced directly to the production of goods. For example, raw materials and direct labor are essential in deriving the cost of a product.
- Indirect Costs: These include expenses that are not directly tied to product creation but are necessary for overall operations. Utilities, maintenance, and rent fall within this category.
Other relevant types of costs include:
- Fixed Costs: These costs remain constant regardless of production volume, such as leases and salaried employees.
- Variable Costs: These are directly proportional to production levels. For instance, the more a factory produces, the more it spends on materials.
- Manufacturing Overhead: This encompasses indirect expenses in production. Calculating overhead accurately is vital for determining the overall cost structure of a manufacturing operation.
Understanding these various facets of manufacturing costs is vital for accurate financial reporting and long-term sustainability!
Key Terms and Concepts
Understanding key terms and concepts in manufacturing accounting is essential for grasping the larger financial picture in a manufacturing environment. Accurate accounting enables companies to allocate resources efficiently and effectively. This showcases the need for clarity regarding critical terminology, which directly influences cost management and decision-making processes.
Direct vs.
Indirect Costs
Direct costs are exceptions in manufacturing operations. These costs are easily traceable directly to specific materials or labor associated with a product. For example, the cost of wood used in furniture, or wages of assembly line workers belong here.
Indirect costs, on the other hand, are more complex. They refer to expenses that cannot be specifically tied to a single product. Examples include utilities, rent, and salaries of managers that oversee the facility. Understanding the distinction between these two categories is vital to producing accurate product cost calculations.
- Direct Costs:
- Indirect Costs:
- Directly linked to the production of goods
- Easier to assignment, improving accuracy in financial reporting
- Unique, often requiring predetermined rates for allocation
- Can complicate overall cost structure
In combination, these understandings set the foundation for effective manufacturing budgeting and performance evaluation.
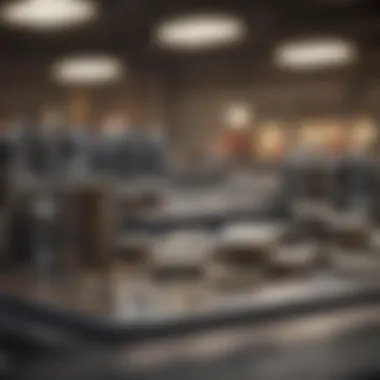
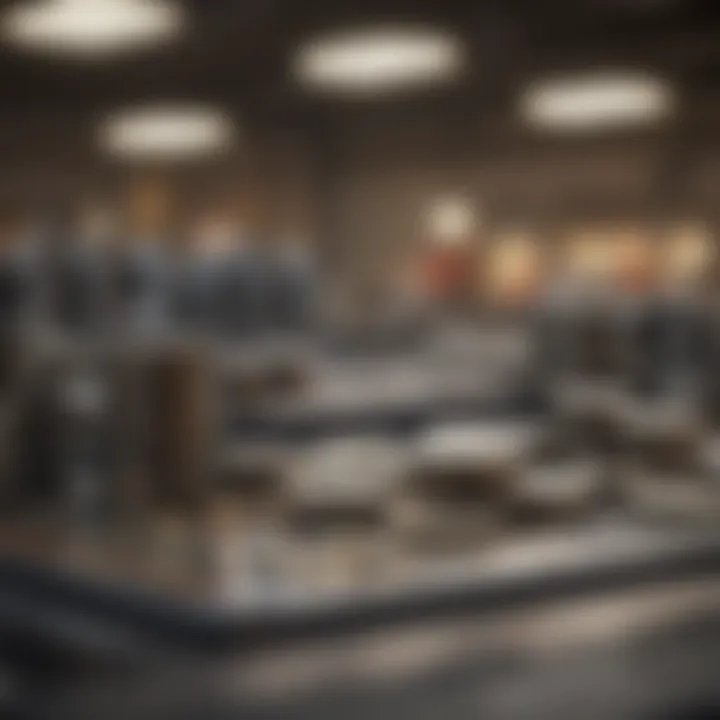
Variable and Fixed Costs
In manufacturing, costs can be categorized as either variable or fixed. Variable costs are expenses that fluctuate with production output; they rise as production increases, and fall when it decreases. Raw materials often fall into this category. For instance, more wires are needed to produce more electronics.
Conversely, fixed costs remain constant regardless of production levels. These typically include expenses such as salaries or mortgage payments for a factory. Recognizing the essense of variable versus fixed costs eases dependency allocation when managing production expenses.
- Variable Costs:
- Fixed Costs:
- Change with output volume
- Important for firms that accelerate or scale back production
- Remain stable no matter how much is produced
- Helps manage long-term roles and responsibilities within units
These classifications are vital for any manufacturing accountant to calculate breakeven points and evaluate overall operational efficiency.
Manufacturing Overhead
Manufacturing overhead encompasses all indirect costs related to production. These are sometimes known as overhead or burden costs. It includes expenses not directly assignable to a finished product, like machinery maintenance or factory supplies. Accounting accurately for manufacturing overhead is crucial for any organization looking to fully understand their production costing.
Proper allocation methods of manufacturing overhead can affect profit margins significantly. An incorrect estimation can lead to incorrect pricing strategies, which can affect sales and resources. To elucidate:
- Inclusions in Overhead:
- Depreciation on manufacturing equipment
- Factory rent and utilities
- Salaries related to unsold goods production
Understanding manufacturing overhead is necessary since it impacts total operational costs while giving insights into overall manufacturing process efficiency. An accountant must monitor these constantly.
Effective allocation and tracking of costs can accurately inform business decisions and enhance overall operational efficiency.
The Manufacturing Accounting Process
The manufacturing accounting process plays a critical role in understanding and managing the financial aspects of manufacturing operations. It provides a structured mechanism for gathering, analyzing, and reporting costs associated with producing goods. This process enables manufacturers to ascertain profitability, control expenses, and optimize resource allocation.
A well-defined accounting process helps management make informed decisions. It can regulate efficiency and minimize wastage, which is both valuable for strategic planning and financial sustainability. Recognizing the significance of this process, we will delve deeper into its crucial components.
Gathering Cost Data
Gathering cost data is the foundation of the manufacturing accounting process. This step involves collecting information on both direct and indirect costs associated with manufacturing. Direct costs are expenses that can be directly tied to the production of specific goods. This includes materials purchased, labor costs, and any resources specifically utilized for manufacturing individual products.
Indirect costs, however, do not encompass direct allocation. These can include utilities, rent, administrative expenses, and other overheads that support the manufacturing process but cannot be directly assigned to specific products. Tracking and documenting all relevant costs ensure accurate calculations of product cost and ultimately affects pricing strategies and profit margins. Getting cost data consistent and precise can decrease monetary risks in operations.
Allocating Costs
Once the cost data is gathered, the next critical step is allocating costs appropriately. Cost allocation presents a challenge since expenses often do not apply to a single end product only. For example, how do you distribute the costs of a fully operational facility among various products being produced?
Allocating costs requires a well-thought-out methodology. Manufacturers often choose allocation methods based on the nature of the business and its products. It can include various techniques such as:
- Activity-based costing: This involves allocating costs based on activities that drive costs in the production process.
- Traditional allocation methods: This is separating overhead based on predetermined rates per machine hour or labor hour.
Proper cost allocation results in accurate product pricing. Without appropriate allocation, a manufacturer may struggle to ascertain which products are profitable and which are not, leading to financial turmoil.
Financial Statements in Manufacturing
Balance Sheet
The balance sheet represents a snapshot of a manufacturing company's financial stance at a particular point in time. In simple terms, it illustrates what the company owns versus what it owes. Its key characteristic lies in detailing assets, liabilities, and shareholder equity, enabling stakeholders to ascertain company health.
The balance sheet is a beneficial choice in manufacturing accounting as it provides clarity on the company's material resources and confirms if obligations, such as loans against utilized credits, are manageable. A unique feature of the balance sheet lies in its informational power. While it consolidates data for period-end accounting, insights into working capital can reveal liquidity risks that could affect place beneficial growth opportunities.
Income Statement
Next, we have the income statement, which captures a manufacturer’s revenue and expenses over a specific period. This documentation can portray monthly sales performance or long-term profits trends. The classical companion, revenues and expenses are akin to two sides of a scale, causing it to lean in either direction based on operational success.
Being insightful as an overview of earnings potentially targeted artificial pricing compliance for pricing models, the income statement helps evaluate how effectively costs are managed to maximize profitability. Knowing whether income overshadows costs explains success. Its limitations could arise from overlooking other costs leading to total operational costs hence why it should efforts to optimization in focus to narrow gross profit.
Cash Flow Statement
The cash flow statement complements income statements by cataloging the actual liquidity of a company and its related operations. It provides insights into how cash moves in and out through operational, investing, and financing activities and highlights whether the organization maintains enough cash to cover daily operating expenses, attract persistent investments, etc.
This statement demonstrates the company's ability to generate cash and is essential for long-term viability. While an impressive net income might showcase optimism, it's equally crucial to decipher whether that's enough cash to run the manufacturing shop appropriately. Relying solely on the cashflow statement in planning might deter attention away from areas necessitating workings funds as requisite productivity to secure lasting growth must forever accentuate efficiency.
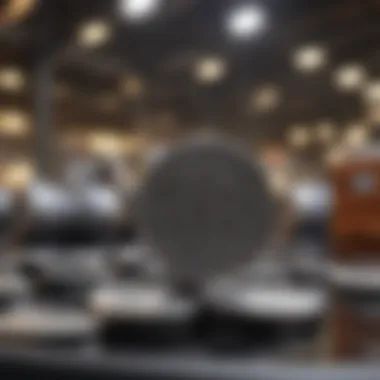
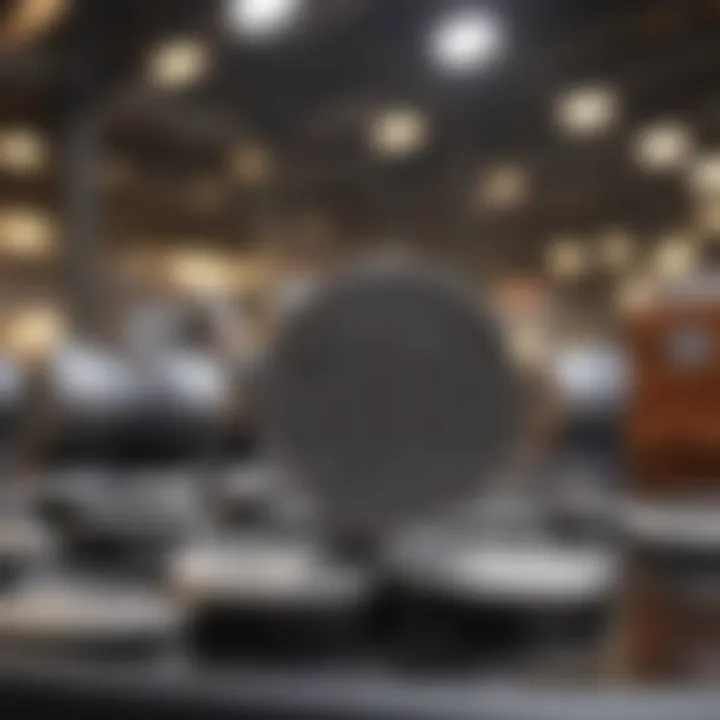
Cost Accounting Methods
Cost accounting methods are vital to manufacturing accounting. They provide a framework for identifying, measuring, and analyzing costs associated with production processes. Understanding these methods guides managers in making informed decisions. Each method has its strengths and weaknesses, depending on the specific business environment and objectives.
Job Order Costing
Job order costing is a method used where products are manufactured based on specific customer orders. Each job is treated independently, and costs are accumulated separately for each job. This is particularly relevant when output is unique or low volume.
Key Features:
- Customization: Allows for precise tracking of costs linked to individual customer specifications.
- Flexibility: Easily adaptable for varying types of orders.
- Detailed reports: Enhances visibility on profitability per job.
Examples of industries where job order costing is paramount include construction, custom furniture production, and specialized manufacturing.
Process Costing
Process costing is used when similarities exist in products being produced. Costs are accumulated for each department or a specific process. This method smooths out costs to achieve an average per unit cost.
Key Attributes:
- Mass Production: Suitable for industries with continuous production like chemicals, stones, and textiles.
- Efficiency: Simplifies accounting records by averaging costs over large volumes.
- Understandable data: Allows clear profitability analysis over extended periods.
Visualizing total costs and dividing them by total units produced allows management to efficiently analyze overall production costs.
Activity-Based Costing
Activity-based costing (ABC) aims at allocating costs to specific activities. Unlike traditional costing methods, ABC assigns costs more accurately based on activities required for production.
Advantages of ABC:
- Precision: Reflects actual resource usage more accurately, leading to improved margin tracking.
- Cost control: Identifies inefficiencies in operations, allowing for optimization.
- Informed decisions: Provides clearer financial insight for pricing, budgeting, and strategic planning.
While ABC offers in-depth analysis, it may also increase complexity in cost allocation, requiring ongoing assessment of activities and costs.
Understanding the right accounting method can make a difference. Each serves distinct needs in manufacturing, crucial for sound financial management.
Budgeting in Manufacturing
Budgeting stands as a pillar in manufacturing accounting. It serves as a strategic tool for planning financial resources, optimizing production costs, and setting measurable targets. An accurate and well-planned budget helps a manufacturing firm to anticipate costs, control expenditures, and enhance profitability. Furthermore, budgeting enables manufacturers to prepare for uncertain economic climates by forecasting needs and allocating funds to essential areas such as materials, labor, and overheads.
In the fiercely competitive manufacturing sector, the ability to manage a budget affects overall business performance. Failing to budget efficiently may lead to over-expenditure or detrimental cuts that affect product quality. Conversely, a precise budget lays the foundation for clear financial tracking, empowering managers to make informed decisions and adjustments throughout the manufacturing process. As a results, improved budgeting contributes to both short-term efficiency and long-term financial health.
Creating a Manufacturing Budget
Creating a manufacturing budget is a multi-step process. It requires a comprehensive understanding of organization priorities, production capacity, and available resources. Begin by estimating sales forecasts, to identify expected revenue streams. Ensure these forecasts include seasonal fluctuations and economic trends that may influence demand.
Next, identify the direct and indirect costs associated with production. This clickable breakdown outlines the vital elements:
- Material Costs: Include raw materials, components, and supplies.
- Labor Costs: Factor in wages, payroll taxes, and employee benefits.
- Overhead Costs: Account for rent, utilities, and equipment depreciation.
The results of these calculations form a detailed budget, enabling managers to examine variances as the production year progresses. After creating the budget, it is important to monitor it continuously. This is essential because expenses often fluctuate, and maintaining flexibility is crucial to adapt when necessary.
Variance Analysis
Variance analysis is a powerful technique in manufacturing accounting that compares budgeted figures to actual outcomes. The main goal of variance analysis is to identify and clarify discrepancies, providing insights into financial performance. This practice can directly affect strategic planning and operational efficiency.
A robust analysis leads to two main types of variances:
- Favorable Variance: Occurs when actual costs are lower than budgeted costs, suggesting an unexpected profit than targeted.
- Unfavorable Variance: Arises when actual costs exceed budget predictions, alerting management to potential issues.
Effective variance analysis involves closely examining causes behind any discrepancies. Factors such as inefficient resource use, unexpected labor costs, or supply chain disruptions should be carefully scrutinized. Understanding these issues can lead to more robust budget expectations in the future.
Regular variance analysis can also reveal trends over time, offering deeper insights into business operations and helping to forecast future budgets more accurately.
Conclusively, budgeting and variance analysis, when conducted in concert, form an integral part of successful manufacturing operations. Effective budget management has the potential to streamline costs, maintain competitiveness, and enable informed decision-making in an increasingly complex environment.
Financial Forecasting for Manufacturing
Financial forecasting plays a crucial role in manufacturing accounting. It helps businesses anticipate future financial outcomes based on historical data and market conditions. Implementing effective forecasting methods can lead to informed decision-making, better resource allocation, and enhanced strategic planning.
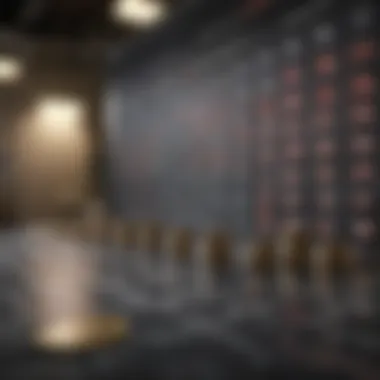
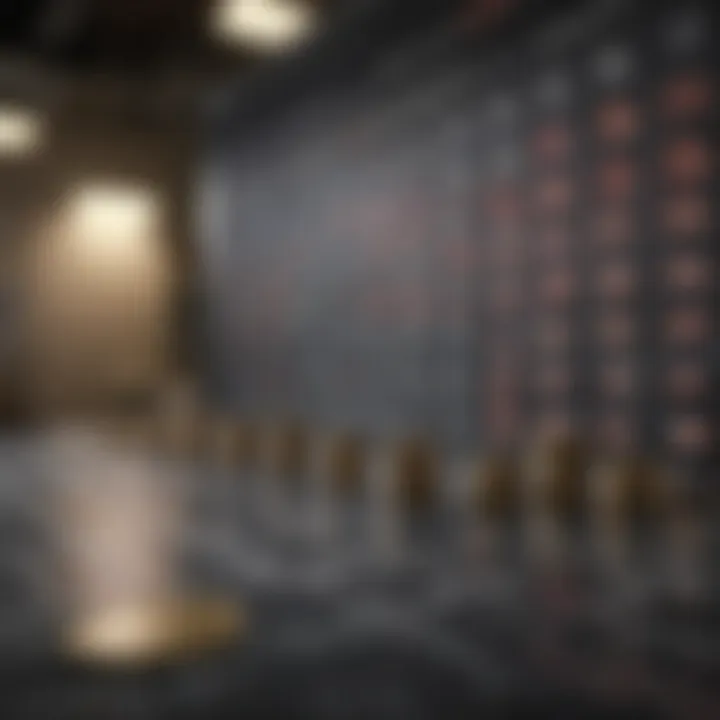
Importance of Forecasting
Forecasting is essential for several reasons. It provides a roadmap for future expenses and revenues. Companies need to know when they will need cash to cover operational costs or invest in new projects. This information influences a range of day-to-day decisions from hiring to inventory management. A well-constructed forecast can also help isolate trends, allowing businesses to adjust their strategies proactively rather than reactively. Moreover, it can be an important tool for identifying cost-saving opportunities, helping firms optimize their manufacturing processes to maximize profitability.
Effective forecasting assists in budgeting and setting realistic operational goals. It is not merely about predicting revenue, but also understanding overall market conditions that influence manufacturing efficiency and costs.
Methods of Forecasting
Forecasting methods can broadly be categorized into two major types: qualitative and quantitative forecasting. Each has its own clarity, landscape, benefits, and drawbacks—which need to be evaluated carefully to choose techniques that best serve a company's specific goals.
Qualitative Forecasting
Qualitative forecasting mainly relies on subjective judgment, opinions, and market research to predict future trends. It is specifically useful in new product launches or when historical data is sparse. Key characteristic of this method is that it incorporates qualitative factors like customer insights, expert opinions, and competitive activity. While it is popular for scenarios lacking quantitative data, the drawbacks include potential biases and lack of statistical rigor.
Advantages of Qualitative Forecasting:
- Utilizes insights from industry experts.
- Especially helpful when drawing upon local market conditions or customer preferences.
- Ideal for new projects without established trends.
However, businesses using this method must exercise caution. Reliable sources of information are key to minimizing bias and ensuring outcomes are as accurate as possible.
Quantitative Forecasting
Quantitative forecasting utilizes numerical data, patterns, and statistical methods to project future financial conditions. Its key characteristic is the use of historical datasets, thus allowing for precise predictions based on actual numbers. This method is beneficial for established companies with access to substantial historical data. It is apparent that a major advantage of quantitative forecasting is the objective nature of its results.
Advantages of Quantitative Forecasting:
- Can produce highly precise forecasts based on vetted historical data.
- Reduces subjectivity and human error, promoting factual accuracy.
- Clear formulas make this method easy to replicate and communicate amongst teams.
That said, the use of purely quantitative forecasts might miss external factors that could impact results, necessitating a combination of both quantitative and qualitative inputs for the most balanced approach.
In summary, understanding both forecasting methods enhances the grasp on manufacturing accounting, empowering managers and stakeholders with reliable data to forge effective business strategies. This dual approach ensures a nuanced strategy tailored to industry circumstances.
Challenges in Manufacturing Accounting
Common Pitfalls
Manufacturing accounting is often fraught with challenges that can impede financial clarity and decision-making. One major issue is accurate cost allocation. Misallocating costs can lead to distorted product pricing strategies. Many firms do not fully understand their cost structures, which disregard crucial components like overhead. Additionally, failure to track indirect costs may result in underestimating total production costs, affecting profits.
Another common pitfall is the oversight of continuous updating of financial systems. Outdated software can misrepresent financial positions by failing to include newer variables or changes in the supply chain. Companies may not consider their unique operational contexts, implying that one-size-fits-all solutions are risky. Lagging information seriously affects budgeting and forecasting processes. Thus, being equipped with the right knowledge and tools is essential. Finally, many small companies ignore regulatory obligations, risking fines or other penalties that come from inadequate accounting practices.
Technological Impact
Technology is transforming the framework of manufacturing accounting, presenting both challenges and solutions. The integration of enterprise resource planning (ERP) systems can improve data accuracy and streamlining processes. However, it can also introduce risks if the implementation process is inadequate. This reliance on technology makes accounting practices vulnerable to technical failures and cyber attacks. Firms obtain vast data, but the have difficulties in ensuring this data is error-free.
Moreover, with the introduction of complex modules in accounting software, staff may not fully utilize all the available functionalities. If employees do not receive adequate training, they cannot maximize their investments in software. Balancing traditional practices with technological advancements can appear daunting but is crucial for sustainable accounting practices in manufacturing. Adaptability becomes necessary, as the landscape of technology shifts rapidly. Organizations must allocate resources towards continuous training and updates in software functionalities. Overall, the technological impact must be recognized and strategically navigated to enhance accountability and efficacy within manufacturing accounting.
Closure
The conclusion of this article ties together the complex aspects of manufacturing accounting, offering a distilled view of its significance. By understanding manufacturing accounting, individuals can make informed decisions around cost management and financial performance. It is essential to recognize that analyzing costs is not just about number-crunching. It is about harnessing data to drive business operation effectiveness.
In addition to comprehending the numbers, engaging with the intricacies of designing budgets and systems for forecasting reinforced the importance of strategic financial planning. The methodologies discussed enrich the decision-making process and contribute to the financial health of an organization in manufacturing, a sector prone to variations.
"Effective manufacturing accounting facilitates not only day-to-day operations but also long-range planning, a vital factor for sustainability."
Key Considerations:
- Ensure understanding of key concepts.
- Leverage budgeting and forecasting techniques.
- Acknowledge possible challenges and pitfalls.
By implementing the guidance offered within this article, you can cultivate a strong foundation in manufacturing accounting. This knowledge ultimately empowers management, leading to improved business modalities and growth opportunities in today’s competitive environment.
Recap of Key Concepts
Reflecting on the fundamental ideas discussed throughout this article, we emphasized several significant components of manufacturing accounting. These include recognizing and distinguishing between direct and indirect costs, the essential nature of variable and fixed costs, and the recognition of manufacturing overhead. These elements serve as the backbone for the financial infrastructure within a manufacturing context.
The approaches to cost accounting including job order costing, process costing, and activity-based costing were explored in detail, exposing their relevance and applications.
Critical concepts in financial forecasting and budgeting, alongside strategies for variance analysis, provide a clearer roadmap for operational efficiency. Each aspect layers together to cultivate an overall understanding of how manufacturing accounting operates within real-world scenarios, showcasing its practicality and essentiality.
Further Resources for Learning
Knowledge in manufacturing accounting can be complemented by various learning resources. Engaging with these materials can undoubtedly deepen understanding and elevate proficiency:
- Books and Texts: Literature on financial management specifically tailored for manufacturing contexts will offer broader insights and case studies.
- Online Courses: Several platforms provide online courses that cover core accounting principles, financial management, and production economics.
- Articles: Websites like Britannica and Wikipedia offer accessible information to expand your knowledge.
- Forums and Communities: Participating in discussions on subreddits like r/accounting can connect you with a community of learners and experienced professionals.
As you navigate the nuances of manufacturing accounting, focusing on continuing your education is vital. Each of these resources contributes to growing financial literacy and understanding of the broader field.