Mastering Inventory Optimization: A Comprehensive Guide for Businesses
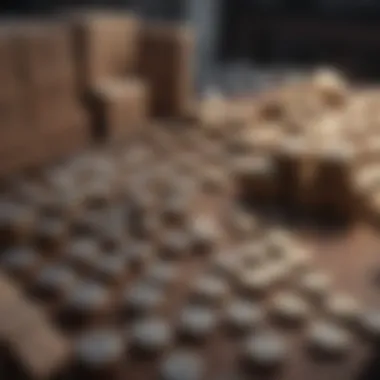
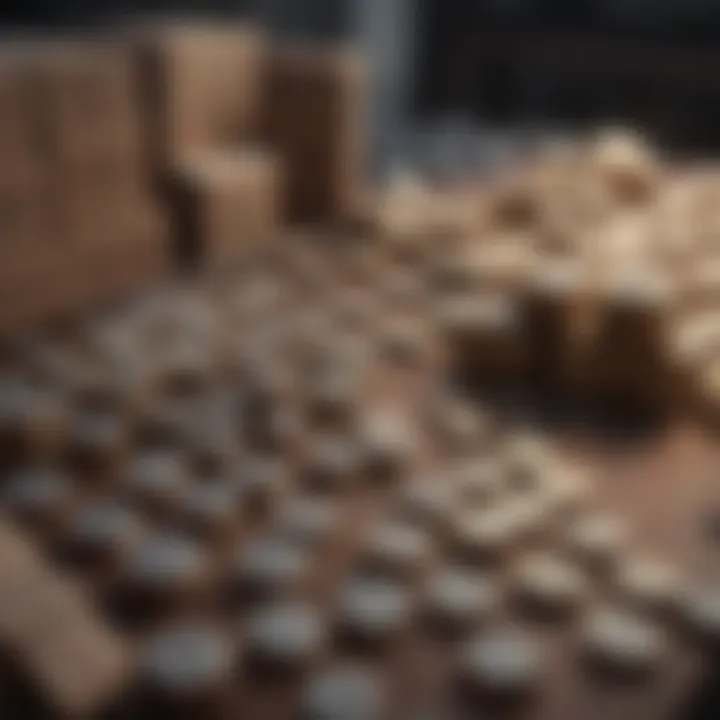
Budgeting Techniques
Developing a personal budget is the cornerstone of effective financial management. By meticulously tracking expenses and setting realistic financial goals, individuals can gain control over their monetary resources. Cultivating a habit of monitoring one's expenditure ensures full awareness of where each penny is allocated. This practice fosters accountability and highlights areas where adjustments can be made for optimal financial health.
Savings Strategies
Building an emergency fund is a prudent step towards financial resilience. By automating savings contributions, individuals can effortlessly set aside a portion of their income for unexpected circumstances. Exploring diverse saving accounts allows for tailored strategies based on individual preferences and objectives. Each account type offers unique features that cater to specific financial needs, providing flexibility in saving methodologies.
Smart Spending Tips
Distinguishing between needs and wants is paramount in cultivating a mindful approach to spending. Leveraging cashback and rewards programs maximizes purchasing power, offering incentives for everyday transactions. Engaging in comparison shopping for significant purchases empowers consumers to make informed decisions, ensuring optimal value for their expenditure. By honing these practices, individuals can make deliberate and strategic choices in their spending habits.
Investment Insights
Deciphering the array of investment options available is crucial for diversifying one's financial portfolio. Understanding the nuances of different investment vehicles enables individuals to make informed decisions aligned with their risk tolerance and financial goals. Efficiently managing risk and return empowers investors to optimize their investment strategy, balancing potential gains with prudent risk mitigation measures.
Financial Planning for the Future
Preparing for long-term financial stability involves comprehensive financial planning for future milestones. Delving into retirement planning basics equips individuals with the knowledge and tools to navigate post-employment years confidently. Considering estate planning ensures smooth wealth transfer and asset protection for future generations. Regularly reviewing and adjusting financial plans is essential for adapting to dynamic life circumstances and staying on track towards financial security.
Introduction:
Inventory management is a crucial aspect of efficient business operations. In this comprehensive guide, we delve deep into the intricacies of developing an inventory reduction plan template. By streamlining inventory processes, businesses can significantly enhance operational efficiency. Effective inventory management is the cornerstone of a well-functioning supply chain, impacting various aspects of a company's financial health and overall performance.
Understanding Inventory Management:
Key Concepts of Inventory Management:
Inventory management encompasses a range of essential principles aimed at optimizing a company's inventory levels. This segment explores the fundamental aspects of inventory control, such as demand forecasting, order quantity optimization, and inventory turnover rates. Understanding these key concepts is critical for maintaining adequate stock levels while minimizing holding costs and stockouts.
Significance of Inventory Optimization:
Inventory optimization plays a pivotal role in enhancing operational efficiency and customer satisfaction. By strategically managing inventory levels, businesses can improve order fulfillment rates, reduce lead times, and enhance overall supply chain performance. This section highlights how inventory optimization aligns with broader organizational goals and enhances the competitiveness of a company in dynamic markets.
Challenges in Inventory Management:
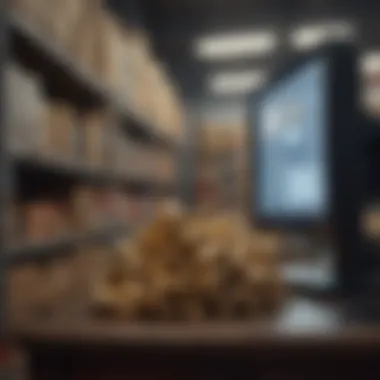
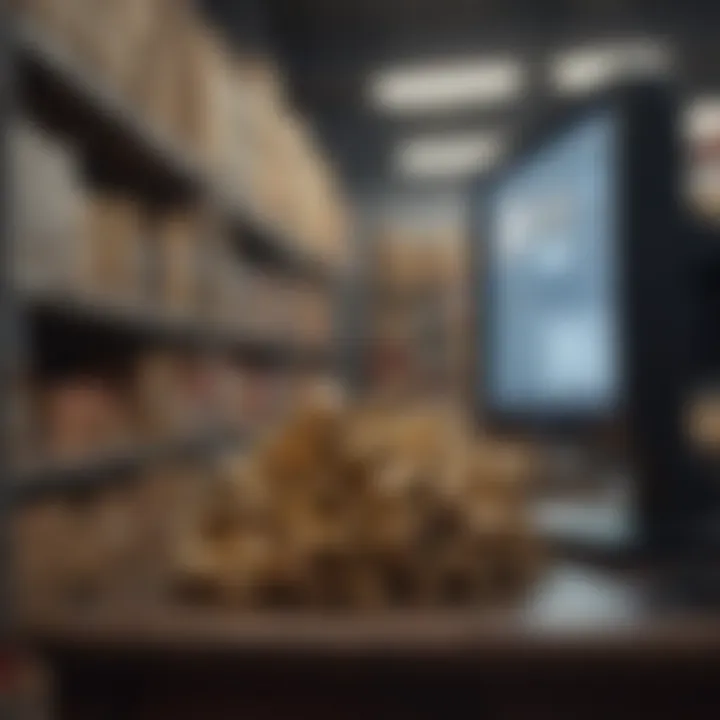
Overstocking:
Overstocking poses a significant challenge for businesses, leading to increased storage costs, inventory obsolescence, and cash flow constraints. This subsection delves into the detrimental effects of overstocking on a company's operational efficiency and financial health. Strategies to mitigate the risks associated with overstocking are essential for maintaining lean inventory levels.
Stockouts and Forecasts Inaccuracy:
Stockouts and inaccuracies in demand forecasting can result in lost sales opportunities and decreased customer satisfaction. This section discusses the repercussions of stockouts and forecast inaccuracies on a company's bottom line and market reputation. Implementing robust forecasting models and agile inventory replenishment strategies is crucial for mitigating these risks.
Importance of Inventory Reduction Plan:
Enhancing Cash Flow:
Efficient inventory management directly impacts a company's cash flow by minimizing working capital tied up in excess inventory. Enhancing cash flow through optimized inventory practices allows businesses to allocate resources efficiently, pursue investment opportunities, and navigate economic uncertainties with greater resilience. Balancing inventory levels with demand fluctuations is key to sustaining healthy cash flow.
Improving Profit Margins:
By reducing inventory carrying costs and obsolescence risks, businesses can improve profit margins and maximize profitability. This subsection explores how inventory reduction strategies contribute to boosting profitability through cost savings, efficient resource allocation, and improved demand forecasting accuracy. A well-crafted inventory reduction plan is vital for enhancing the financial performance of a company.
Developing an Inventory Reduction Plan
Developing an Inventory Reduction Plan is a pivotal aspect of operational excellence in the realm of inventory management. Within the scope of this article, the focus lies on delineating concrete steps for businesses to strategically diminish excess inventory and optimize operational efficiency. By comprehensively addressing the nuances of inventory reduction planning, organizations can enhance their financial well-being and streamline their processes effectively to align with market demands and trends.
Assessment of Current Inventory
Inventory Audit
In the realm of assessing current inventory, the Inventory Audit stands as a cornerstone element. This meticulous process involves scrutinizing existing stock levels, evaluating storage conditions, and cross-referencing physical inventory against digital records. Within this article, the Inventory Audit holds substantial importance as it serves as the bedrock for understanding inventory discrepancies, identifying surplus stock, and rectifying inventory management inefficiencies. Its unique characteristic lies in its ability to provide a snapshot of a business's current inventory status, facilitating informed decision-making. Despite its manual nature, the Inventory Audit proves beneficial in uncovering discrepancies and improving inventory accuracy.
Demand Forecasting Analysis
On the other hand, Demand Forecasting Analysis plays a critical role in predicting future inventory requirements based on historical data and market trends. Pertaining to the overarching goal of inventory reduction, Demand Forecasting Analysis guides businesses in optimizing stock levels, reducing excess inventory, and meeting customer demand efficiently. Its unique feature lies in its ability to anticipate fluctuations in demand, aiding in proactive inventory management. While advantageous in offering insights for strategic decision-making, Demand Forecasting Analysis may face challenges in accurately predicting demand fluctuations in volatile market conditions.
Setting Inventory Reduction Goals
Defining Target Inventory Levels
In the pursuit of inventory reduction, defining Target Inventory Levels serves as a fundamental aspect. This process involves setting optimal stock thresholds that align with demand patterns, production constraints, and storage capacities. Within this article, the significance of Defining Target Inventory Levels lies in providing a tangible roadmap for inventory optimization, cost reduction, and operational efficiency. Its unique characteristic is its ability to establish clear guidelines for stock control and inventory replenishment, mitigating the risk of stockouts or overstocking. Despite its advantages in promoting inventory visibility and control, setting stringent Target Inventory Levels may pose challenges in accommodating demand fluctuations.
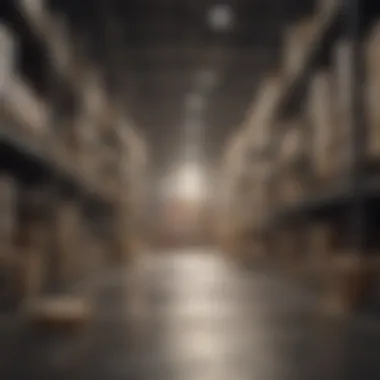
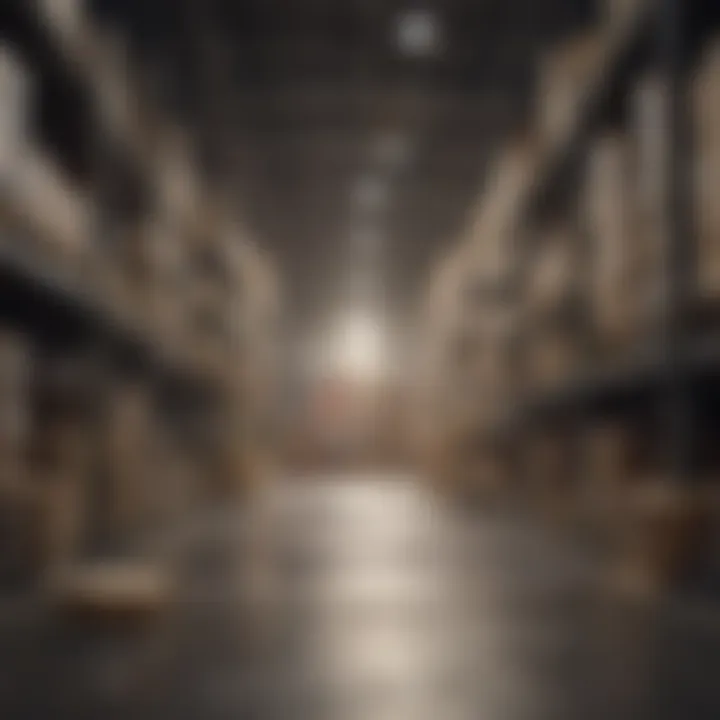
Establishing Monitoring Metrics
Complementing the establishment of Target Inventory Levels is the task of Establishing Monitoring Metrics. This involves defining key performance indicators (KPIs) and metrics to track inventory turnover, stock accuracy, and order fulfillment rates. In this article, Establishing Monitoring Metrics plays a vital role in evaluating the effectiveness of inventory reduction strategies, identifying operational inefficiencies, and fostering continuous improvement. Its unique feature lies in providing real-time insights into inventory performance, facilitating data-driven decision-making. While advantageous in enhancing inventory transparency and accountability, Monitoring Metrics may encounter limitations in capturing the holistic impact of external market dynamics on inventory operations.
Implementing Strategies for Reduction
Just-In-Time Inventory System
At the core of inventory optimization strategies is the implementation of the Just-In-Time Inventory System. This methodology emphasizes replenishing stock only when needed to minimize excess inventory, storage costs, and wastage. In the context of this article, the Just-In-Time Inventory System emerges as a preferred choice for businesses seeking lean inventory management and operational efficiency. Its unique feature lies in promoting workflow efficiency, reducing lead times, and enhancing resource utilization. While advantageous in promoting cost savings and responsiveness to demand fluctuations, the Just-In-Time Inventory System may face challenges in adjusting to sudden demand spikes or supply chain disruptions.
ABC Analysis
Moreover, ABC Analysis offers a structured approach to categorizing inventory based on value and turnover frequency. By segmenting inventory into categories A (high value, low quantity), B (moderate value, moderate quantity), and C (low value, high quantity), businesses can prioritize resource allocation and inventory management efforts. In the context of this article, ABC Analysis stands out as a practical tool for identifying critical inventory items, optimizing stock levels, and reducing carrying costs. Its unique feature lies in segmenting inventory based on strategic importance, facilitating better decision-making around stock replenishment and storage. While advantageous in focusing resources on high-value items, ABC Analysis may encounter challenges in dynamically classifying items based on fluctuating market demands.
Utilizing Technology for Optimization
Inventory Management Software
Streamlining inventory management processes, Inventory Management Software plays a pivotal role in automating stock tracking, order processing, and inventory valuation. By centralizing inventory data, generating real-time reports, and streamlining supplier interactions, Inventory Management Software enhances operational efficiency and inventory visibility. Its unique feature lies in improving inventory accuracy, minimizing manual errors, and accelerating order fulfillment processes. While advantageous in enhancing inventory control and streamlining workflows, Inventory Management Software may confront challenges in compatibility issues with existing systems and high implementation costs.
RFID Technology Implementation
Furthermore, RFID Technology Implementation revolutionizes inventory tracking and management through radio frequency identification tags. By enabling precise stock monitoring, automated inventory counts, and real-time asset tracking, RFID technology enhances inventory visibility and supply chain efficiency. Within this article, RFID Technology Implementation emerges as a cutting-edge solution for improving inventory accuracy, minimizing stock shrinkage, and enhancing warehouse operations. Its unique feature lies in providing real-time inventory updates, reducing human error in stock counts, and optimizing inventory replenishment. While advantageous in boosting inventory visibility and operational transparency, RFID Technology Implementation may face challenges in initial investment costs and integration complexities with existing inventory systems.
Monitoring and Adjusting the Plan
In this detailed section, we unravel the crucial importance of Monitoring and Adjusting the Plan within the overarching theme of optimizing inventory management. By carefully monitoring and flexibly adjusting the inventory plan, businesses can stay resilient and efficient in their operations. This process involves constant vigilance, data-driven decision-making, and strategic adaptations to ensure optimal inventory levels.
Regular Performance Evaluation
KPIs Tracking
Let's delve into one cornerstone of inventory management - Key Performance Indicators (KPIs) Tracking. KPIs serve as compasses, guiding businesses in assessing performance and progress towards objectives. Within the context of this article, KPIs Tracking enables companies to measure crucial metrics such as turnover rates, holding costs, and customer satisfaction levels. The distinctive aspect of KPIs Tracking lies in its ability to offer real-time insights, helping stakeholders make informed choices promptly.
On the flip side, the overreliance on KPIs alone may lead to tunnel vision, overlooking intangible factors vital for organizational success. Balance is key, ensuring KPIs Tracking supplements but doesn't overshadow strategic intuition.
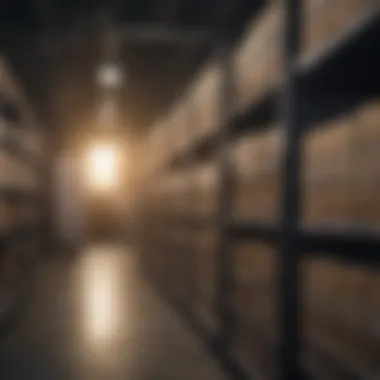
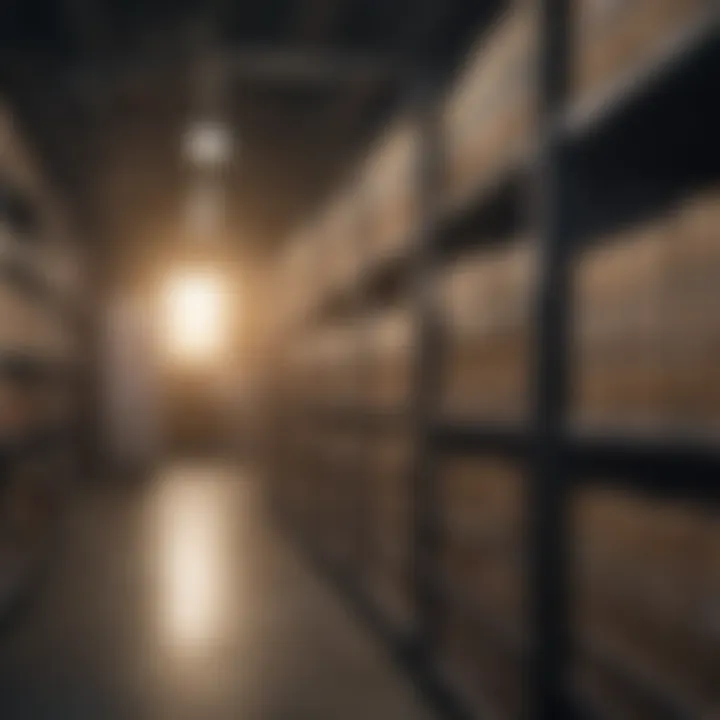
Continuous Improvement Strategies
Another pivotal aspect within the realm of regular performance evaluation is Continuous Improvement Strategies. These strategies catalyze growth and efficiency, driving businesses towards excellence. For our audience endeavoring operational efficacy, incorporating Continuous Improvement Strategies like Kaizen methodology or Six Sigma can foster a culture of continuous enhancement.
Continuous Improvement Strategies shine in their adaptability, allowing businesses to evolve in dynamic market landscapes. However, too rapid changes may disrupt workflows, necessitating a delicate equilibrium between constancy and evolution.
Flexibility and Adaptability
Responding to Market Trends
Flexibility within inventory management extends to Responding to Market Trends. This facet accentuates the significance of agility in adapting to evolving market dynamics. Businesses must keenly observe market fluctuations and promptly realign inventory strategies to match consumer demands and trends. In our article, we highlight how adeptly responding to market trends can position businesses favorably in competitive marketplaces.
However, hyper-responsiveness may drive businesses to erratic decision-making, jeopardizing long-term stability for fleeting gains. Striking a harmonious chord between responsiveness and prudence is key for sustained success.
Supply Chain Optimization
Last but not least, Supply Chain Optimization emerges as a linchpin in inventory management flexibility. Efficient supply chain networks streamline operations, reducing lead times and costs while enhancing overall efficiency. The allure of Supply Chain Optimization lies in its capacity to synchronize various aspects of operations, harmonizing inputs and outputs seamlessly.
Nonetheless, an overly optimized supply chain may breed vulnerabilities, amplifying risks of disruptions during unforeseen circumstances. Cultivating a resilient, rather than just optimized, supply chain is paramount for enduring operational success.
Conclusion
In the realm of inventory management optimization, the conclusion serves as a pivotal point of reflection and application. This section encapsulates the key takeaways and actionable insights gleaned throughout the article, emphasizing the criticality of strategic inventory practices in streamlining operations and bolstering efficiency. By scrutinizing the nuances of inventory reduction plans and delving into the intricacies of demand forecasting, businesses can pave the way towards sustainable growth and profitability. The conclusion acts as a compass, guiding organizations towards operational excellence and competitive advantage in a dynamic market landscape by embracing forward-thinking inventory management methodologies.
Achieving Operational Excellence
Sustainable Inventory Practices
Sustainable inventory practices epitomize the ethos of balance and efficiency within operational frameworks. By focusing on minimizing waste, optimizing storage processes, and maximizing resource utilization, businesses can foster resilience and agility in their inventory management strategies. The hallmark of sustainable inventory practices lies in their ability to not only reduce costs but also mitigate environmental impact, aligning with the paradigm shift towards eco-conscious operations. This conscientious approach to inventory management confers a dual benefit of cost savings and environmental stewardship, positioning businesses as ethical entities while improving operational efficacy.
Competitive Advantage
Competitive advantage acts as a fulcrum in the realm of inventory management, delineating the thin line between success and stagnation in fiercely competitive markets. By leveraging strategic inventory practices, organizations can outpace rivals, capture market share, and fortify customer loyalty. The essence of competitive advantage lies in its capacity to differentiate businesses from counterparts through unique value propositions, operational efficiencies, and customer-centricity. Embracing innovative inventory strategies empowers firms to navigate uncertainties, capitalize on emerging trends, and carve a niche that resonates with discerning customers, shaping a sustainable growth trajectory.
Future of Inventory Management
Emerging Technologies Impact
The emergence of cutting-edge technologies catalyzes a paradigm shift in conventional inventory management paradigms, ushering in an era of digitization, automation, and predictive analytics. Harnessing the potential of emerging technologies empowers organizations to optimize Supply Chain Management, enhance inventory visibility, and streamline order fulfillment processes with unparalleled precision and velocity. The crux of the impact of emerging technologies lies in their propensity to revolutionize traditional inventory paradigms, augmenting decision-making prowess, and catalyzing leaner, more responsive supply chains that adapt to market exigencies with dexterity.
Industry Best Practices
Industry best practices serve as beacons of guidance and benchmarks for excellence in the realm of inventory management optimization. By benchmarking against industry stalwarts, adopting proven methodologies, and aligning with prevailing benchmarks, organizations can fortify their operational frameworks, mitigate risks, and drive continuous improvement. The essence of industry best practices lies in their universal applicability, scalability, and adaptability across diverse business sectors, rendering them indispensable tools for enhancing operational efficiency, resilience, and customer satisfaction.